Introduction:
Production and efficiency are critical in today’s dynamic warehouse and distribution environments. The utilization of tugger trains is one invention that has gained pace and is revolutionizing the handling of goods within these facilities. These adaptable and automated solutions have changed the game by providing a host of advantages that boost productivity and streamline processes.
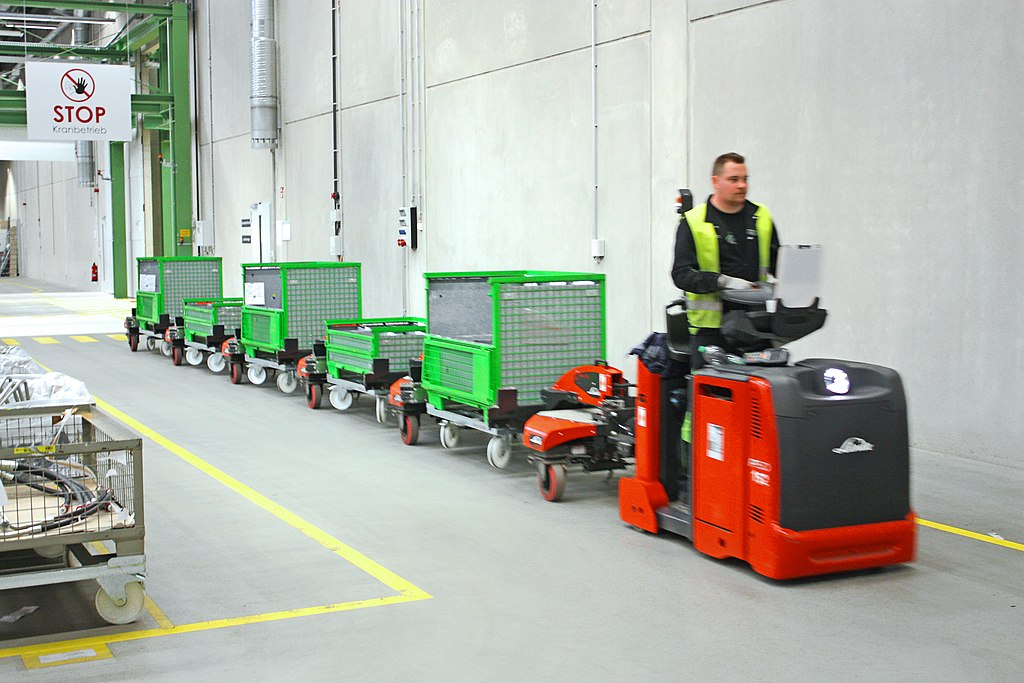
Understanding Tugger Trains:
Automated guided vehicles (AGVs) such as tugger trains are used in warehouses and manufacturing facilities to move supplies, merchandise, and parts. In contrast to conventional forklifts and human material handling techniques, tugger trains follow pre-planned paths that are detected by sensors or magnetic strips inserted into the ground. Because to this technology, movement may be done precisely and predictably, which lowers the chance of accidents and raises workplace safety standards.
Key Features and Components:
- Tugger Units: The tugger units, which are small, electric-powered vehicles with the capacity to tow many carts or trailers behind them, are the fundamental components of the tugger train system. Because these devices are programmable and simple to connect with current warehouse management systems, collaboration and communication are made possible with ease.
- Carts and Trailers: Usually, a tugger train consists of several trailers or carts pulled behind the tugger unit. Because these carts are made to carry particular kinds of materials or items, they may be used in a wide range of applications and industries. Because the system is modular, it may be easily customized to meet the specific needs of any site.
- Control System: The tugger train’s control system functions as its brain. It oversees the connection between the central warehouse management system, carts, and tugger units. Real-time material tracking, optimized traffic flow, and effective routing are all made possible by this centralized control.
Benefits of Tugger Trains:
- Increased Efficiency: Because tugger trains are meant to run constantly, they cut down on the downtime that comes with manual material handling. The system’s automation guarantees a steady and predictable flow of supplies, which boosts warehouse operations’ overall efficiency.
- Flexible and Scalable: The adaptability and scalability of tugger trains is one of their best qualities. Facilities may readily modify the system to meet changing demands because to its modular architecture. As the need for material transport grows, they can add more tugger units, reprogramme routes, or change the number of carts.
- Enhanced Safety: In every warehouse environment, safety comes first. By removing the need for physical material handling and lowering the danger of accidents related to forklifts and other conventional techniques, tugger trains help to create a safer work environment. Workplace safety is further improved by collision avoidance systems and predetermined routes.
- Cost-Effective: Long-term cost reductions are large with tugger train systems, even if the initial expenditure may appear high. For facilities that use tugger trains, the efficiency gains, labor cost reductions, and decreased risks of product damage result in a rapid return on investment (ROI).
- Improved Ergonomics: Because tugger trains lessen the physical strain on warehouse workers, they improve ergonomics. An more pleasant and effective work environment results from staff being able to concentrate on more value-added duties like inventory management, quality control, or strategic planning thanks to automated material transfer.
Case Studies and Success Stories:
With impressive outcomes, a number of warehouses and distribution facilities have already used tugger train technology. Case studies from a range of sectors demonstrate the beneficial effects on effectiveness, security, and overall operational excellence.
- E-commerce Fulfillment Center: A significant online retailer increased order fulfillment speed by thirty percent by using tugger trains in its fulfillment facility. The system’s adaptability to handle a wide variety of items was one factor in the implementation’s success.
- Automotive Manufacturing Plant: Tugger trains were used in an automobile manufacturing plant to move parts from the warehouse to the assembly line. Because of the system’s flexibility, lead times were shortened and production efficiency increased as a result of its ability to quickly adapt to changes in production schedules.
Read More: The Future of Smart Speed Bump
Read More: High-Performance Concrete Build Business Case Value