Coupling Rebar
Coupling Rebar Reinforced concrete structures rely heavily on rebar for strength and durability. When constructing large buildings, bridges, and other infrastructure, rebar needs to be connected securely to ensure structural integrity. This is where coupling rebar comes into play.
Rebar couplers have revolutionized the construction industry by providing a strong, efficient, and cost-effective alternative to traditional lap splicing. If you’re wondering what coupling rebar is, how it works, and why it’s important, this guide will cover everything you need to know.
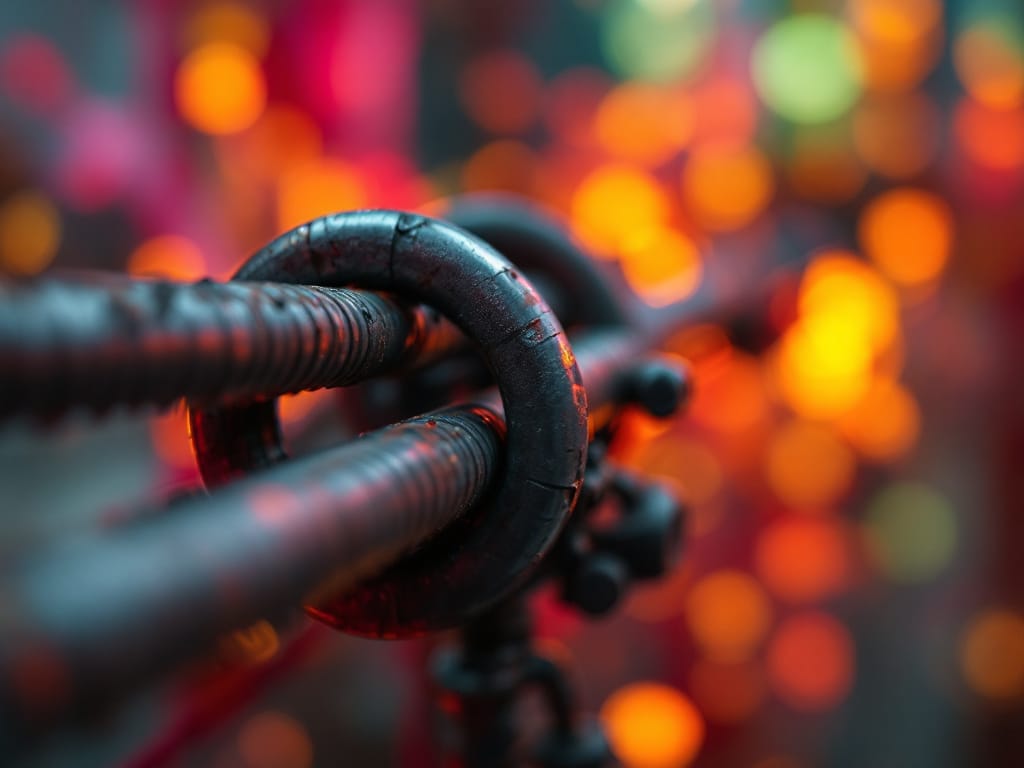
What is Coupling Rebar?
Coupling rebar, also known as a rebar coupler or mechanical splicing, is a method used to connect two reinforcement bars without overlapping them. Instead of lapping the rebar, a coupler—a mechanical device made of steel—is used to join the ends of two rebars, ensuring a strong and continuous connection.
This technique enhances the efficiency of construction projects by reducing material waste, saving labor costs, and improving the overall strength of reinforced concrete structures.
Why is Coupling Rebar Important?
Traditional rebar connection methods, such as lap splicing, can lead to material wastage and require more space. Rebar couplers eliminate these issues while providing several advantages, such as:
1. Stronger Structural Integrity
Rebar couplers create a direct and solid connection between bars, reducing weak points in the concrete structure. Unlike lap splicing, which depends on overlapping bars, couplers ensure better load transfer.
2. Reduced Rebar Usage
Lap splicing requires additional length to overlap the bars, increasing material costs. By using rebar couplers, the required length is minimized, leading to material savings.
3. Faster Construction Time
Since rebar coupling eliminates the need for overlapping, it simplifies the construction process. This results in faster installation times, allowing projects to stay on schedule.
4. Space Efficiency
In high-rise buildings and complex structures, rebar congestion can be a problem. Couplers reduce congestion by allowing bars to be joined end-to-end, making reinforcement placement more efficient.
5. Greater Seismic Resistance
In earthquake-prone areas, structures must withstand high levels of stress. Rebar couplers enhance seismic performance by providing a continuous load path, improving the building’s stability.
Types of Rebar Couplers
Rebar couplers come in different types, depending on their design, application, and the type of connection required. Below are the most commonly used rebar coupling methods:
1. Threaded Rebar Couplers
- Uses a threaded sleeve to connect two rebars.
- Requires threading the ends of the rebars before inserting them into the coupler.
- Provides high strength and reliability.
2. Mechanical Rebar Couplers
- Uses a mechanical locking system to join rebars.
- Ideal for high-stress applications, such as bridges and skyscrapers.
- Eliminates the need for threading, reducing preparation time.
3. Weldable Rebar Couplers
- Designed for applications where rebar needs to be welded.
- Suitable for structures that require both mechanical and welded connections.
4. Grout-Filled Couplers
- Uses high-strength grout to bond the rebar inside the coupler.
- Often used in precast concrete structures and repairs.
5. Compression Couplers
- Uses mechanical pressure to hold the rebars in place.
- Does not require threading or welding.
Each type of coupler has its specific advantages, and the choice depends on factors like load requirements, environmental conditions, and project specifications.
How to Install Rebar Couplers
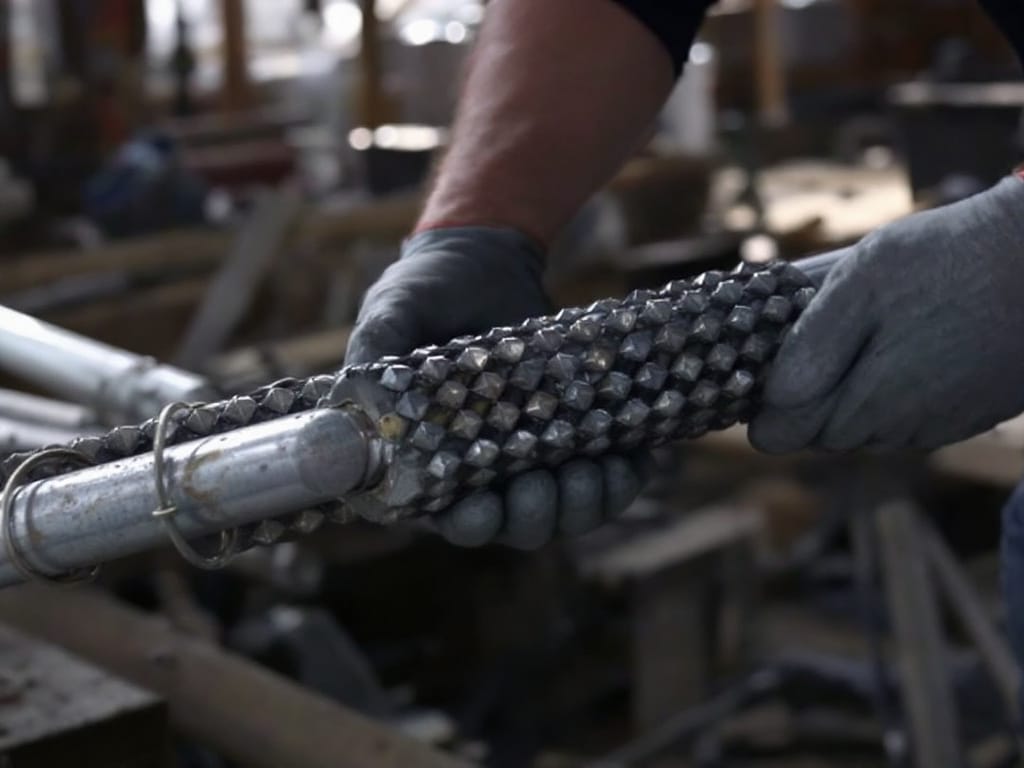
Installing rebar couplers requires precision to ensure a strong and reliable connection. Here’s a step-by-step guide:
Step 1: Prepare the Rebar Ends
Ensure that the rebar ends are clean and cut properly. If using threaded couplers, the ends must be threaded according to the coupler specifications.
Step 2: Insert the Rebar into the Coupler
Place the rebar ends into the coupler, ensuring they fit securely. Some couplers require manual tightening, while others may use specialized tools.
Step 3: Tighten the Coupler
For mechanical or threaded couplers, use a torque wrench to tighten the connection according to the manufacturer’s specifications. This ensures the coupler is securely fastened.
Step 4: Inspect the Connection
Check for any misalignment or loose fittings. The connection should be firm, with no visible gaps between the rebar and the coupler.
Step 5: Pour the Concrete
Once all couplers are installed and secured, proceed with the concrete pouring process. Ensure that the couplers remain in position during pouring.
Applications of Coupling Rebar
Rebar couplers are used in various construction projects, particularly where high-strength reinforcement is required. Some common applications include:
🏗 High-Rise Buildings – Helps reduce rebar congestion and allows for efficient load transfer.
🌉 Bridges and Overpasses – Provides superior strength and resistance to heavy loads and environmental stress.
🚆 Railway and Metro Projects – Used in tunnels and tracks where reinforced concrete is critical.
🏥 Hospitals and Seismic-Resistant Buildings – Improves structural integrity in earthquake-prone zones.
🏢 Precast Concrete Structures – Allows for easy connection between precast elements.
Rebar Coupling vs. Traditional Lap Splicing
Feature | Rebar Coupling | Lap Splicing |
Material Usage | Less rebar required | Requires extra overlap length |
Strength | Higher load capacity | Less efficient load transfer |
Installation Time | Faster installation | More labor-intensive |
Cost Efficiency | Saves material and labor costs | Higher rebar usage increases costs |
Space Efficiency | Reduces rebar congestion | Can be difficult to manage in tight spaces |
Rebar coupling is clearly the better choice when it comes to efficiency, strength, and cost-effectiveness.
Factors to Consider When Choosing Rebar Couplers
When selecting a rebar coupler, consider the following factors:
✅ Project Requirements – Ensure the coupler meets the strength and load-bearing capacity needed.
✅ Rebar Size Compatibility – Different couplers are designed for specific rebar diameters.
✅ Environmental Conditions – For projects in corrosive environments, use couplers with anti-corrosion coatings.
✅ Ease of Installation – Some couplers require specialized tools, while others offer a simple mechanical connection.
✅ Regulatory Compliance – Check whether the coupler complies with building codes and industry standards.
Where to Buy Rebar Couplers
Rebar couplers are available at:
🏢 Construction Supply Stores – Many physical stores carry a range of couplers for different applications.
💻 Online Suppliers – Websites like Amazon, Alibaba, and industry-specific suppliers offer bulk purchasing options.
🏗 Direct Manufacturers – Purchasing directly from manufacturers ensures high-quality and certified products.
Always verify product specifications before making a purchase to ensure compatibility with your project requirements.
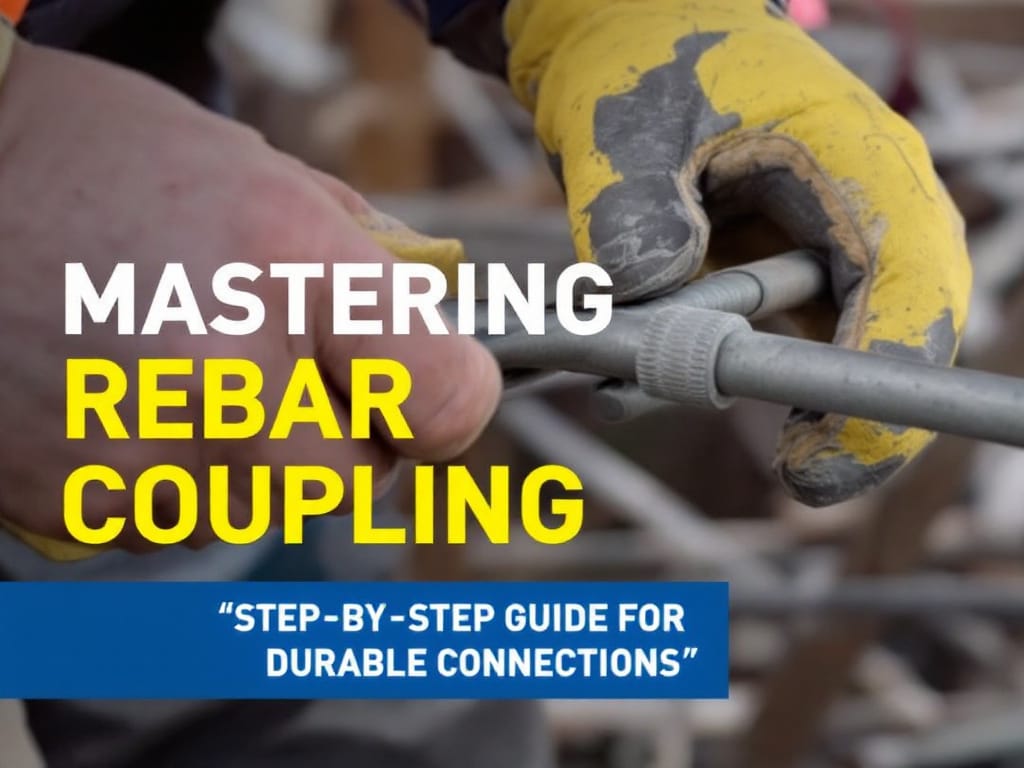
Final Thoughts
Coupling rebar is a game-changer in modern construction, offering superior strength, efficiency, and durability compared to traditional lap splicing. Whether you’re working on a high-rise building, a bridge, or a seismic-resistant structure, rebar couplers provide a reliable and cost-effective solution.
By understanding the different types of couplers, their applications, and proper installation techniques, you can ensure a seamless construction process with improved structural performance.
So, if you’re looking for a stronger, smarter, and more efficient way to connect rebar, investing in high-quality rebar couplers is the way forward!
Read More: The Future of Smart Speed Bump
Read More: High-Performance Concrete Build Business Case Value